Services
CASIN by SANEON: the unique solution for CAD-CAE data exchange
Time is money. You can save both by using our novel CASIN platform. CASIN produces time gains of more 99 % during CAD-CAE data exchange.
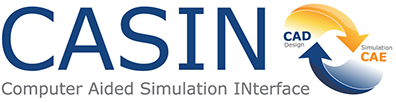
CASIN – computer-aided simulation interface (CASIN) – facilitates the cross-domain, bidirectional and automated transfer of CAD data between construction and simulation environments. What’s more, the entire process is done without integrity losses. All it takes is a press of a button, and CAD information (kinematics, etc.) can be transmitted directly from CAD environments to MATLAB. The result is a complete multi-body simulation model.
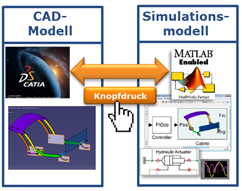
How does CASIN work? The software automatically transfers knuckle joints, inertia tensors, body visualization and user-defined parameters into a simulation-capable Simulink model. The simulation can then be analyzed with the help of functions provided by MATLAB / Simulink, e.g., in terms of the input power of the actuators. The user-defined parameters can be manipulated from MATLAB in CATIA. The geometry via MATLAB-integrated optimization functions can then be completed. The short throughput times for transmission enable kinematics to be validated at an early development stage.
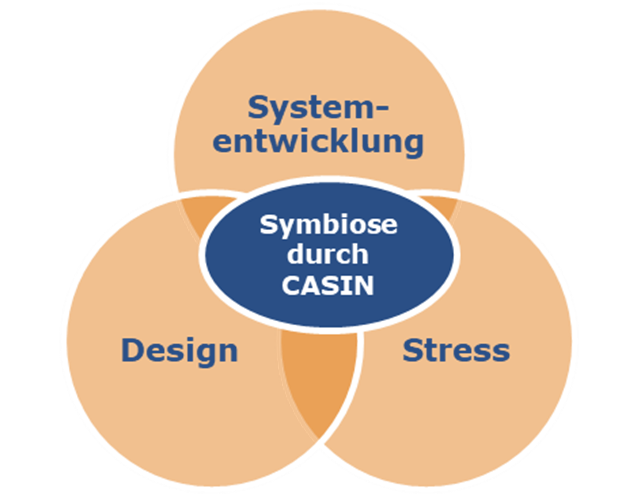
Other CASIN features include product optimization (weight, power consumption, system performance, etc.), the determination of the entire system’s behavior during an early development phase, virtual validation through automatic collision detection and a faster time to market.
CASIN is a true innovation, one that significantly lowers the costs of generating simulation models and facilitates a high degree of system understanding at an early stage as a result – the total amount of time saved adds up to 99 %.
Contact calculation for complex surfaces (CONICS)
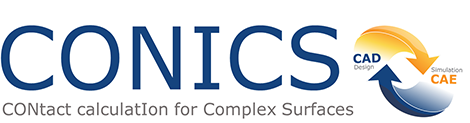
Up to now, Simulink has been unable to calculate contact forces between arbitrary bodies in a multi-body simulation. This functional shortcoming is eliminated by our CONICS software.
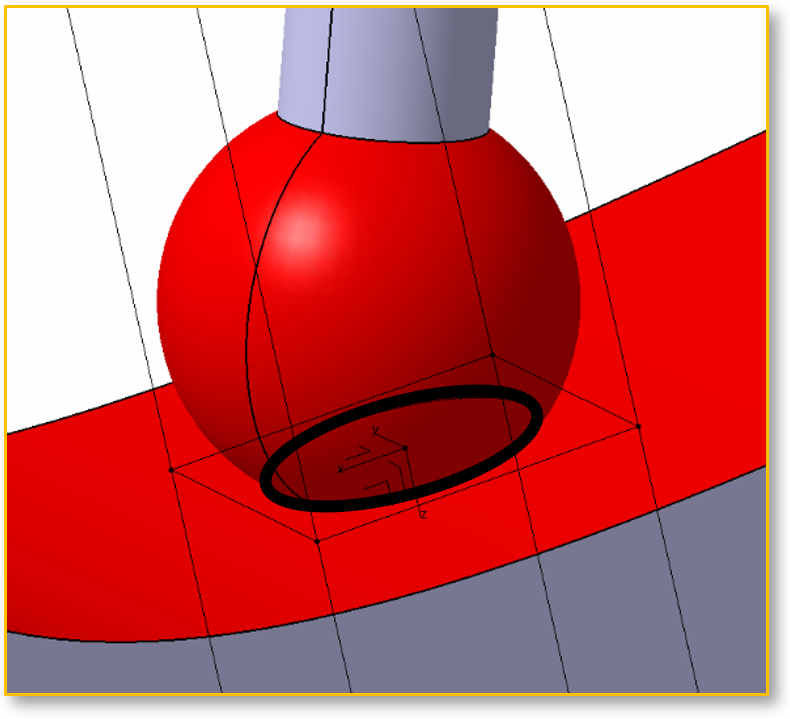
With the help of CONICS, the surfaces developed in CAD are exported with a very high level of detail and are then stored in MATLAB / Simulink. During the simulation, the bodies are checked for overlapping during a hardware-accelerated process (with the help of the GPU of simulation computer). In the process, the contact force model may also be applied. The contact force model can also take friction in such places as the contact into consideration.
The simulation itself is performed independently of the CAD suite. The results of the contact force analysis can be exported and then analyzed by the user with the help of the wide range of models available in MATLAB.
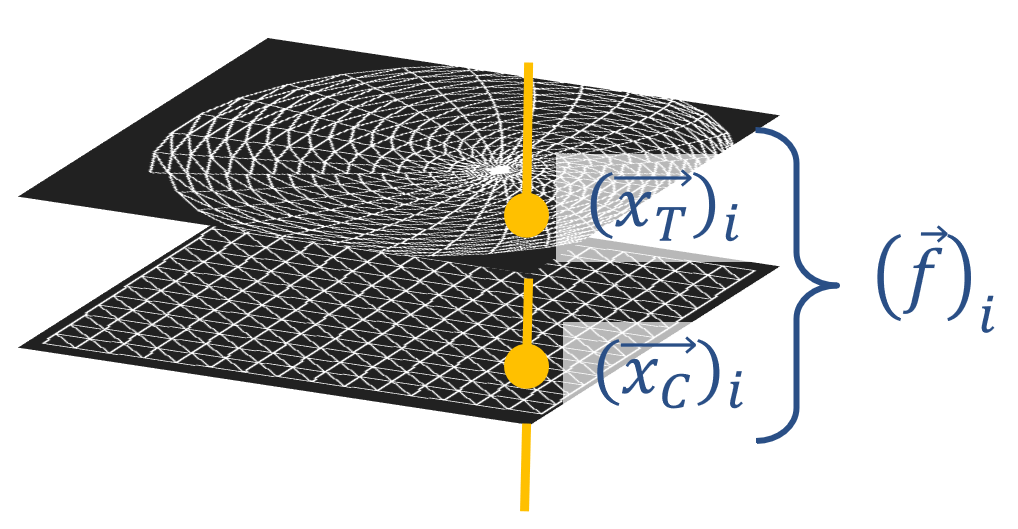
Geometric optimization of the contact surfaces can also be done in connection with CASIN. Using parameters in the CAD system, the geometry of the contact surface is deliberately changed by one of the optimization algorithms to minimize the established cost function.
Results can be quickly achieved through hardware acceleration. This, in turn, makes it possible to examine the suitability of various types of contact surfaces without using prototypes.
Our innovation facilitates the creation of extremely detailed simulations of body contacts in Simulink that also take friction into account without the need to do any extensive setup work. These findings can then be used to devise operation characteristics at an early stage and modify them if necessary.
Contact:
Other topics: